Efficient warehouse management is crucial for optimizing operations, reducing costs, and ensuring customer satisfaction. However, many businesses unknowingly make mistakes that can lead to inefficiencies, delays, and unnecessary expenses. Understanding these common errors can help you refine your processes and improve overall productivity.
By recognizing and addressing these six common warehouse management mistakes, businesses can enhance efficiency, reduce costs, and improve overall productivity. Implementing smart solutions and maintaining a well-organized warehouse can make all the difference in achieving long-term success.
1. Poor Inventory Tracking
One of the most frequent issues is poor inventory management, leading to overstocking, stockouts, or inaccurate record-keeping. Without real-time tracking and proper categorization, warehouses struggle to maintain efficiency. Another common mistake is neglecting organization and storage solutions. A well-structured warehouse with optimized shelving, storage bins, and an industrial cabinet for tools and equipment can significantly enhance workflow and accessibility.
Lack of Real-Time Stock Updates
Failing to update stock levels in real time causes discrepancies. Missing or excessive stock due to outdated records leads to delays and inefficiencies in order fulfillment. Implementing barcode or RFID scanning ensures that inventory records remain accurate, preventing costly errors. Additionally, cloud-based inventory systems provide instant updates, making it easier to track stock levels across multiple locations.
Inefficient Inventory Audits
Skipping regular inventory audits leads to errors. Physical counts help reconcile system data against actual stock, ensuring accuracy in warehouse management and customer order processing. Cycle counting—where inventory is audited in sections on a rotating basis—reduces disruptions while maintaining high accuracy. Businesses that prioritize frequent inventory checks can better identify slow-moving stock and adjust procurement strategies accordingly.
2. Ineffective Warehouse Layout
Poor Space Utilization
Wasting space reduces storage efficiency. A disorganized layout increases retrieval times, leading to delays in processing and shipping customer orders. Implementing vertical storage solutions, such as mezzanines or high-density shelving, can help maximize available space. Efficient slotting techniques, where items are strategically placed based on demand frequency, can also speed up retrieval.
Lack of Clearly Defined Zones
Without distinct zones, workers waste time searching for items. Defining sections for receiving, picking, and shipping improves workflow and minimizes confusion. Color-coded signage, automated guided vehicles (AGVs), and digital mapping tools help create a structured warehouse layout. A well-defined zoning strategy ensures that high-priority items remain accessible while reducing unnecessary travel within the warehouse.
3. Inadequate Staff Training
Insufficient Process Familiarity
Employees unfamiliar with warehouse processes slow operations. Proper training ensures workers understand procedures, reducing errors in order picking and inventory handling. Training programs should also include cross-training strategies, allowing employees to perform multiple roles as needed, which enhances workforce flexibility during peak seasons.
Lack of Safety Protocol Knowledge
Uninformed staff are prone to accidents. Training employees on safety measures prevents injuries and ensures compliance with workplace regulations. Regular safety drills, clear hazard markings, and proper use of personal protective equipment (PPE) significantly reduce workplace incidents. Investing in ongoing safety training minimizes liability risks and fosters a safer work environment.
4. Poor Demand Forecasting
Overestimating or Underestimating Stock Needs
Ordering too much or too little disrupts business operations. Overstock leads to wasted storage, while understock frustrates customers with unavailable products. Leveraging predictive analytics tools can help businesses accurately forecast demand based on historical data, market trends, and seasonal patterns.
Ignoring Seasonal Demand Changes
Failing to anticipate seasonal fluctuations causes lost sales and excess stock. Analyzing past trends helps maintain optimal stock levels year-round. Businesses should establish supplier relationships that allow for flexible inventory scaling, ensuring they can quickly adjust stock levels based on changing consumer demand.
5. Inefficient Order Processing
Lack of Automation in Order Handling
Manual order management is slow and error-prone. Integrating automated systems speeds up processing and minimizes mistakes in shipping and fulfillment. Voice-picking technology, robotics-assisted sorting, and AI-driven packing solutions can further optimize the fulfillment process.
In addition, failing to implement automation and technology often results in slow operations and human errors. Modern warehouse management systems (WMS) can streamline order fulfillment, automate inventory updates, and increase accuracy. Inefficient layout planning is another critical problem, as poor spacing and disorganized pathways lead to wasted time and increased labor efforts.
Poor Picking and Packing Strategies
Unoptimized picking routes and inefficient packing methods delay deliveries. Organized workflows ensure faster, more accurate order fulfillment. Implementing batch picking or zone picking methods can streamline retrieval, while using standardized packing procedures reduces material waste and enhances shipment protection.
6. Neglecting Regular Maintenance
Failing to Inspect Warehouse Equipment
Ignoring regular equipment maintenance leads to breakdowns. Unexpected malfunctions disrupt workflow and cause costly downtime in operations. Scheduled maintenance programs for forklifts, conveyors, and automated storage systems help prevent sudden failures and extend equipment lifespan.
Overlooking Software Updates
Outdated warehouse management software creates inefficiencies. Regular updates ensure smooth system performance, improving inventory tracking and order management. Cloud-based WMS platforms provide real-time synchronization, making it easier to scale operations as business needs evolve.
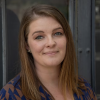
Lynn Martelli is an editor at Readability. She received her MFA in Creative Writing from Antioch University and has worked as an editor for over 10 years. Lynn has edited a wide variety of books, including fiction, non-fiction, memoirs, and more. In her free time, Lynn enjoys reading, writing, and spending time with her family and friends.