Choosing the right banding system can significantly impact operational costs and efficiency when setting up packaging operations. Many manufacturers want to understand the power differences between heat seal and ultrasonic systems to decide which technology better suits their needs. What power requirements differ between heat seal and ultrasonic banding machines?
Heat seal banding systems typically require 800-1200 watts of power, while ultrasonic systems operate more efficiently at 400-600 watts, making ultrasonics approximately 50% more energy-efficient.
While this basic power consumption comparison is helpful, it must tell the complete story. Understanding each system’s warm-up times, operational cycles, and peak power demands can dramatically affect total energy costs and production efficiency, so it’s worth delving deeper into these important details.
How Do Warm-Up Times Compare Between These Banding Systems?
Heat seal systems require significant warm-up time, typically 3-5 minutes before being ready for operation. This warm-up period consumes power without producing any output. In contrast, ultrasonic systems are ready almost instantly, requiring no warm-up time and allowing immediate operation when powered on.
These warm-up differences can substantially impact productivity and power consumption for facilities running multiple shifts or having frequent start-stop cycles. A heat seal system might waste up to 30 minutes of power per day in warm-up time across multiple starts.
What Are The Peak Power Demands During Operation?
Heat seal systems experience high power spikes during sealing operations, often drawing 1500-2000 watts momentarily. These power surges can strain electrical systems and may require special circuit considerations. Ultrasonic systems maintain more consistent power usage, with peak demands rarely exceeding 800 watts.
This steady power consumption of ultrasonic systems makes them easier to integrate into existing electrical systems and helps prevent circuit overload issues that sometimes plague heat seal installations.
How Do Operational Cycles Affect Overall Power Usage?
The duty cycle—the percentage of time a system actively seals bands—significantly impacts total power consumption. Heat seal systems continue consuming substantial power (200-300 watts) even when idle to maintain temperature, while ultrasonic systems draw minimal power (less than 50 watts) during idle periods.
This idle power consumption becomes particularly important for operations with irregular production flows or frequent stops. Under the same conditions, a heat seal system running at 50% duty cycle might consume more than three times the energy of an ultrasonic system.
These operational characteristics make ultrasonic systems attractive for facilities with variable production schedules or multiple daily startups.
What Maintenance Requirements Impact Power Usage?
Heat seal systems require regular cleaning of heating elements to maintain efficient power usage. As residue builds up on heating surfaces, these systems often require more power to achieve the same sealing temperature, sometimes increasing power consumption by 15-20% between cleanings.
Ultrasonic systems, with their non-contact sealing mechanism, maintain consistent power consumption regardless of usage duration. This consistency eliminates the gradual power increase often seen in heat seal systems and reduces the frequency of maintenance-related downtime.
Do Environmental Conditions Affect Power Consumption?
Ambient temperature and humidity can significantly impact the power requirements of both systems but in different ways. Heat seal systems require more power to reach operating temperature in cold environments, sometimes needing up to 25% more energy during winter or in air-conditioned spaces.
Ultrasonic systems remain relatively unaffected by environmental conditions, maintaining consistent power consumption across varying temperatures and humidity levels. This stability makes them particularly suitable for facilities with seasonal temperature fluctuations or those operating in challenging environmental conditions.
Heat seal systems may also require supplemental cooling in hot environments to prevent overheating, adding to the overall power consumption. This indirect power cost is often overlooked in initial comparisons but can significantly impact total energy usage in certain climates.
Making Your Decision Count
Before finalizing your banding system selection, analyze your specific production patterns, including the number of daily starts, typical duty cycles, and environmental conditions in your facility. Once you’ve gathered this data, you can accurately calculate the total power costs for each system type, going beyond the basic wattage ratings to include all the indirect power factors we’ve discussed. This comprehensive approach will ensure you make an investment decision based on true operational costs rather than just initial power specifications.
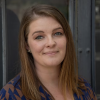
Lynn Martelli is an editor at Readability. She received her MFA in Creative Writing from Antioch University and has worked as an editor for over 10 years. Lynn has edited a wide variety of books, including fiction, non-fiction, memoirs, and more. In her free time, Lynn enjoys reading, writing, and spending time with her family and friends.