Profile extrusion is a sophisticated manufacturing process that produces continuous lengths of material with complex cross-sectional profiles. While it offers remarkable versatility in creating custom shapes for various industries, it also presents unique challenges. This article explores the intricacies of profile extrusion and why many companies are turning to outsourcing to overcome these hurdles.
Understanding Profile Extrusion
Profile extrusion involves forcing molten material, typically plastic, through a die to create a continuous profile with a specific cross-sectional shape. This process is used to manufacture a wide range of products, from window frames and weather stripping to complex automotive components.
Key Challenges in Profile Extrusion
1. Die Design and Manufacturing
One of the most significant challenges of a profile extrusion company is the design and manufacture of the extrusion die. The die must be precision-engineered to create the desired profile shape while considering factors such as material flow, cooling rates, and potential distortion. Even minor flaws in die design can lead to significant quality issues in the final product.
2. Material Selection and Behavior
Different materials behave uniquely during the extrusion process. Factors such as melt viscosity, thermal stability, and shrinkage rates can greatly affect the quality of the extruded profile. Selecting the right material and understanding its behavior under extrusion conditions is crucial for achieving the desired results.
3. Process Parameter Control
Maintaining consistent quality in profile extrusion requires precise control of numerous process parameters. These include extrusion temperature, pressure, cooling rate, and line speed. Balancing these parameters is often a complex task that requires significant expertise and experience.
4. Post-Extrusion Challenges
After extrusion, profiles may require additional processing such as cooling, cutting, and surface treatment. Managing these post-extrusion processes without compromising the profile’s shape or quality presents its own set of challenges.
5. Quality Control and Consistency
Ensuring consistent quality across long production runs is a persistent challenge in profile extrusion. Variations in raw material, environmental conditions, or equipment wear can all impact product quality, necessitating robust quality control measures.
6. Tooling Costs and Lead Times
The custom nature of profile extrusion often requires specialized tooling, which can be expensive and time-consuming to produce. Managing tooling costs and lead times, especially for low-volume or prototype runs, can be challenging for many manufacturers.
Innovations in Profile Extrusion
Despite its challenges, profile extrusion continues to evolve, driven by technological advancements and industry demands. Recent innovations are helping manufacturers overcome some of the traditional hurdles. For example, computer-aided design (CAD) and simulation allow for precise die design, helping predict and mitigate potential issues before physical production begins, reducing trial and error and improving efficiency.
As the technology continues to advance, we can expect to see even more sophisticated and sustainable profile extrusion solutions in the future.
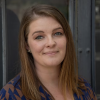
Lynn Martelli is an editor at Readability. She received her MFA in Creative Writing from Antioch University and has worked as an editor for over 10 years. Lynn has edited a wide variety of books, including fiction, non-fiction, memoirs, and more. In her free time, Lynn enjoys reading, writing, and spending time with her family and friends.