Effective cost management in construction projects is crucial for keeping them on budget and meeting their objectives. Whether you are constructing a single-family house or overseeing a large commercial project, controlling costs carefully lets you use your resources wisely and avoid unnecessary delays. With smart practices, you can make budgeting easier, improve resource usage, and keep things clear throughout the project.
Here are some practical ways to manage construction project costs.
Start with a Detailed Budget
Making a solid budget is key to managing costs. A well-thought-out budget includes labour, materials, equipment, and backup funds.
Break down each project stage and set realistic costs for every part. Remember to consider variable expenses like changing material prices or weather delays. Working with your team while budgeting ensures accuracy and sets clear expectations right from the beginning. A detailed budget guides spending and spots cost-saving opportunities before the project begins.
Use Construction Accounting Software
Construction accounting software is a powerful tool for managing project costs accurately and efficiently. These platforms integrate financial data, letting you track expenses, monitor budgets, and create real-time reports.
A major benefit of this software is its ability to work with other project management tools, like scheduling and resource allocation systems. This connection gives you a full view of your project’s financial situation, making pinpointing and fixing any issues more manageable.
Construction accounting software also simplifies tasks like invoicing, payroll, and vendor payments. By automating these processes, you can reduce mistakes and save time, allowing you to focus on key project parts. This technology is a vital tool for managing costs effectively for modern construction projects.
Monitor Costs Regularly
Regularly checking on progress is key to managing project expenses. Set up consistent meetings to review spending and see how actual costs match the original budget.
These frequent check-ins help spot any overspending early so you can adjust plans if needed. For example, if material prices are higher than expected, you can look into other suppliers or negotiate better deals. Keeping a watch on your finances also ensures everyone, including team members and vendors, is accountable.
Optimize Resource Allocation
Using resources efficiently can really affect project costs. Effective use of labour, materials, and equipment helps cut down on waste and avoids delays.
Start by putting together a detailed schedule that fits your budget and project timeline. Assign tasks based on the skills and availability of your team members, ensuring everyone is doing work that suits their expertise. For materials and equipment, opt for just-in-time delivery to avoid having too much in stock and reduce storage costs.
Communicate with Stakeholders
Talking openly with stakeholders is essential for managing costs. Keeping everyone updated on the project’s financial situation helps build trust and ensures everyone agrees on goals and expectations.
Have regular meetings to review progress, check spending, and solve any possible issues. Sharing detailed reports with charts or graphs makes it easier for stakeholders to see the project’s financial condition.
When everyone understands what’s happening, decisions are made quicker, lowering the chance of expensive mistakes or miscommunications.
Plan for Contingencies
Unexpected expenses can pop up during construction, no matter how carefully you plan. Setting aside some extra funds allows you to tackle surprises without throwing off your budget.
A smart guideline is to save 5–10% of the total budget for these unexpected costs. This extra money helps you deal with design changes, delays from bad weather, or insufficient materials. A backup plan gives you financial security and lets you adjust when things are unplanned.
Negotiate with Vendors
Building strong ties with vendors can help reduce costs. By negotiating contracts, buying in bulk, or setting up long-term agreements, you can often get better deals on materials and equipment.
Look into multiple suppliers and compare their prices before choosing one. Building a good relationship with vendors might also mean perks like fast delivery or discounts on future projects. Good negotiation helps you get the most value for your money, allowing you to stay within budget without sacrificing quality.
Utilize Preconstruction Planning
Planning before construction starts helps spot ways to save money. This step looks at the project’s design, materials, and if it can be done to keep costs down later. Working with architects, engineers, and contractors at this stage lets you fine-tune the project and stick to the budget.
Using value engineering is often crucial in this process. By spending time on detailed planning, the construction project can run smoother and be more cost-effective.
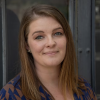
Lynn Martelli is an editor at Readability. She received her MFA in Creative Writing from Antioch University and has worked as an editor for over 10 years. Lynn has edited a wide variety of books, including fiction, non-fiction, memoirs, and more. In her free time, Lynn enjoys reading, writing, and spending time with her family and friends.