Polyamide (PA) is a thermoplastic polymer with multiple industrial applications. There are many types of PA, one of which is well-known: nylon. This article discusses the main PA varieties, such as PA6, PA66, PA11, and PA12, and how they are used in modern engineering.
Background of PA
Unlike wool and silk, nylon is an artificial type of polyamide synthesised from petroleum-based plastics. Nylon was introduced in the market by DuPont during the 1930s as a resistant and cost-effective option to silk stockings. Soon, nylon was everywhere, from clothing to the automotive industry.
While PA and nylon are commonly used as synonyms, there are three polyamide families: aromatic, semi-aromatic, and aliphatic. Nylon and its variants (PA6, PA66, PA11, and PA12) are Aliphatic polyamides, which are known for their strength, durability, flexibility, and thermal resistance.
Main Varieties and Applications
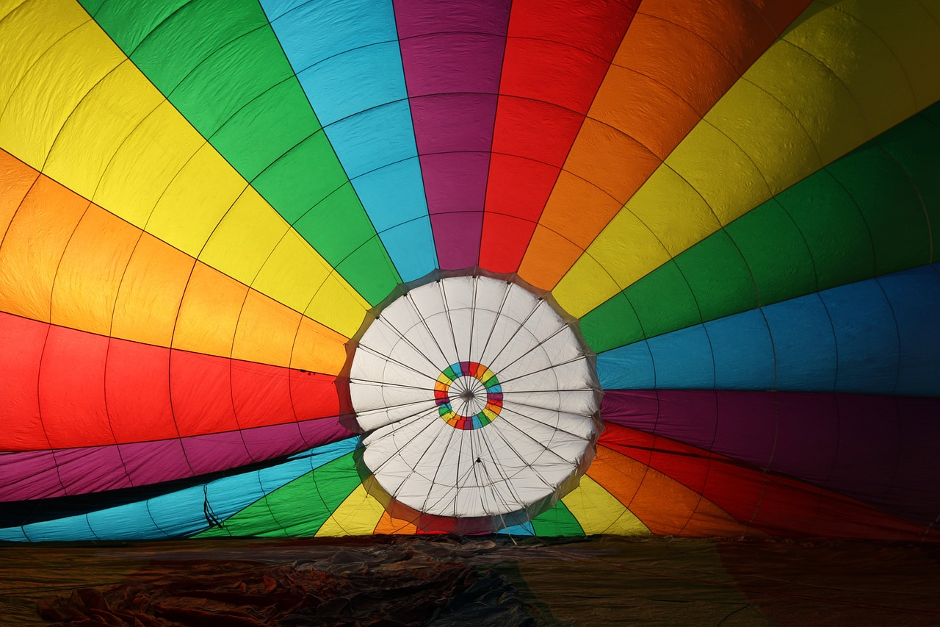
Polyamides are constantly in high demand across several industries. Last year, the polyamide market was valued at USD 25.03 billion, with solid growth projections for the next few years, chiefly when it comes to environmentally friendly options. Here are the most commonly used types of PA.
PA12
PA 12 is a type of semi-crystalline plastic that can be synthesised from petroleum or renewable materials. It’s also a common option for polyamide tubes used in automotive and industrial sectors.
PA11 and PA12 are quite similar in terms of chemical properties. However, PA12 is more suitable for 3D-printed parts for medical applications, such as prostheses. Indeed, it’s a superior option to injection-moulding plastics, given its mechanical properties and weather resistance.
PA6
Polycaprolactam, also known as PA6 or “nylon 6,” is the most common type of PA, with a melting point of 223ºC. This variant is quite resistant to heat, moisture, and chemical abrasion; it’s also perfect for electrical insulation. It’s mostly used in automotive parts, electrical components, and industrial machinery.
PA66
PA66 is a more resistant variety with a melting point of 255ºC. It is made of a combination of adipic acid and hexamethylenediamine. Due to its superior strength and impact resistance, PA66 is used in cable ties and connectors. In vehicles, it can be found on air intake manifolds and engine covers. Its improved moisture resistance means it has much more dimension stability than the P6.
PA11
Unlike most PAs, PA 11 is based on a natural source: the castor plant. It has great elasticity and impact resistance, which is great for crash-relevant car parts. Additionally, it’s resistant to a wide range of chemicals. PA11 is mostly used in functional prototypes for automotive parts. It also has aesthetic use in visible parts since it’s easy to manipulate and handles abrasion quite well.
The Future of Polyamides
The demand for high-performance PA is at an all-time high worldwide and shows no sign of slowing down. It has countless industrial applications, but market projections point to an increasing demand from the electrical and electronics sectors. However, synthetic polyamides will gradually be replaced by more environmentally friendly options, such as bio-polyamides for coating and film applications.
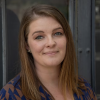
Lynn Martelli is an editor at Readability. She received her MFA in Creative Writing from Antioch University and has worked as an editor for over 10 years. Lynn has edited a wide variety of books, including fiction, non-fiction, memoirs, and more. In her free time, Lynn enjoys reading, writing, and spending time with her family and friends.