It is a fact that Precise threaded holes are a fundamental part of the metal manufacturing process. These holes are crucial for joining metal machinery components with ultimate precision and accuracy. A precisely created threaded hole not only ensures the longevity and reliability of the assembly but also increases its structural integrity. The different types of threaded holes depend upon the material’s properties, the drilling tools, and the application domain of the products being manufactured.
Furthermore, the right understanding of the machining tools, feed rate, and appropriate angle measurements are essential for metal CNC machining services. This article will help you to understand the challenges related to the metal machining of threaded holes and the marvelous engineering behind them.
Drilling Pilot Hole Diameter
The pilot holes act as a guide during the machining process of threaded holes. The choice of appropriate pilot holes depends upon the material being drilled, the thread size, and the pitch. During metal CNC machining, for softer materials, machinists choose to go with a small pilot hole while minimizing the cutting torque. While for harder materials a large pilot hole is machined as it facilitates smoother tapping and ultimately prevents unnecessary tool wear.
Another important factor that defines the pilot hole diameter is thread class, thread class such as 1B, 2B, or 3 B, helps in choosing the right diameter for threaded holes.
For the perfect pilot hole drilling, the most important paramount is the clamping of the workpiece and the right drilling tool. A twist drill bit with a slightly smaller diameter than the required thread size is mostly used for drilling. Once these parameters are set, the drilling begins at a controlled speed and feed rate. A high feed rate in this case can cause excessive heating and may damage the drill bit tool and thread size.
Once the process is started, the drill removes the material in small chips, which are removed consistently by high-speed blown air. If the chips are not properly removed then it may affect the drilling process by affecting the angle of the drill.
Thread’s Depth and Pitch
The deciding factors for precise thread depth are the material’s tensile strength, the diameter of the fastener, and the required load-bearing capacity. By carefully evaluating these factors, engineers can determine ideal thread depths as per their applications, While maintaining the strength, reliability, and efficiency of the thread holes.
In aerospace applications where the machines have to face extreme pressure and vibrations, deeper threaded holes are manufactured, as they enhance thread engagement and prevent loosening over time. This will provide more stability to the machines.
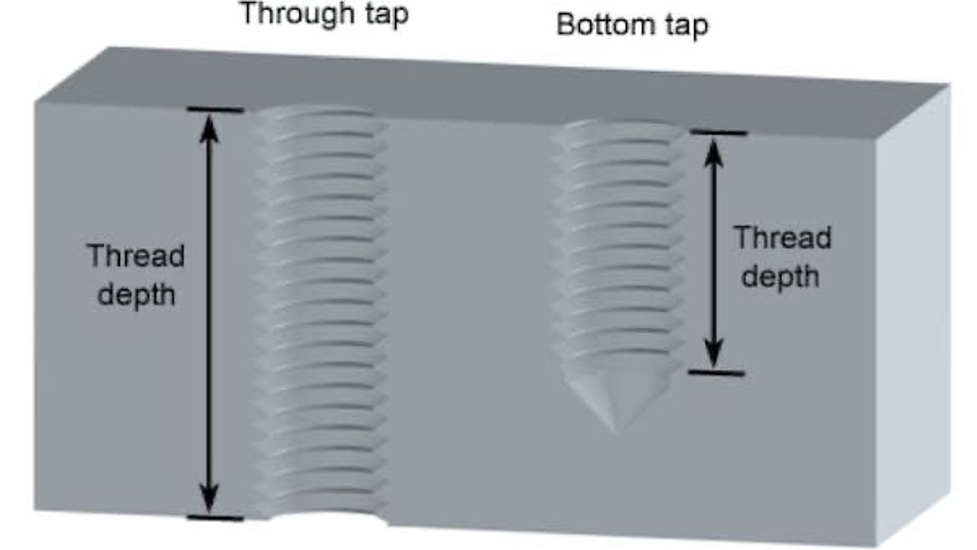
On the other hand, in lightweight applications engineers are concerned with reducing overall weight without affecting the overall structural integrity. For these conditions, minimizing the thread depth can help conserve material. A typical thread depth can be around 1.5 times the fastener, for a smooth engagement and to prevent thread stripping in matting parts.
Now as we talk about pitch considerations the three most important parameters for it are thread engagement, torque requirements, and vibration resistance. Along with these deciding parameters, engineers are concerned about the material’s ductility and the potential for galling or seizing during assembly. In manufacturing two types of pitch geometries are mostly used, which are coarse pitches and Fine pitches.
Coarse pitches are used where one has to concern about, the overall strength and load-bearing capacity of the joint. Coarse pitches have large thread spacing, and they provide deeper engagements of the joints. These are mostly used where one has to deal with high vibration such as heavy ship structures. However, fine pitches are ideal for industries where we have to design complex and intricate structures within the minimum space.
Hardness Of the Material
During the metal manufacturing of threaded holes, the material selection is the most important paramount. Machining harder materials such as titanium, Inconel, and tool steels poses significant challenges due to their extreme hardness, strength, and abrasiveness. For threading these materials, specialized tooling, such as carbide or diamond-coated taps is used. These tools are not only able to withstand high pressure and stress, but they also show less wear and tear during machining.
For Extremely hard such as titanium alloys, the drilling process is quite complicated. By directly implementing machining operations on them the workpiece and the cutting tool may get damaged. To avoid these, engineers recommend going for pre-drilling or pre-tapping procedures. In these techniques a pilot hole is created before threading, the pilot hole ensures precise alignment and reduces cutting force during the final tapping process.
The pre-drilling process involves the creation of a slightly smaller hole with the intended thread diameter. While pre-tapping involves partially threading the hole to guide the tap accurately which will assist in the final threading process. This manufacturing technique is quite evident while machining, engine mounts for the aerospace industry. The titanium mounts are extremely hard to machine, so carbide cutting tools which are precisely engineered with cutting angles and titanium nitride coatings help to achieve reliable thread formations.
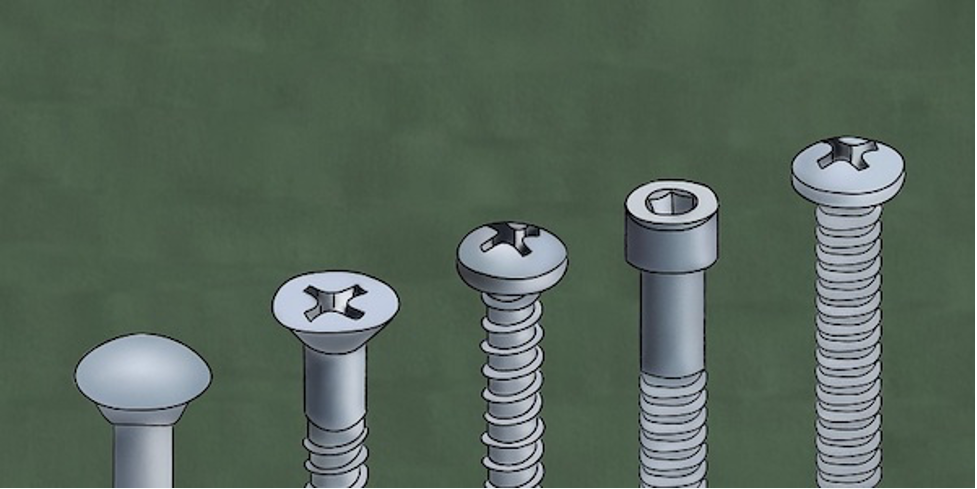
On the other hand, if you are dealing with softer materials like aluminum and brass. The primary concerns are avoiding excessive chip buildup and its removal. The excessive chip formation affects the tool cutting speed, to overcome this specialized high-speed steel (HSS) taps with coatings like titanium nitride (Tin) are used.
Thread Form and Profile Optimization
In heavy automotive and heavy machinery applications, threaded joints due to heavy loads and vibrations have to bear stresses along their connections. Engineers are concerned with minimizing the distribution of stresses along the roots and crests of threads so that they can increase their load-bearing capacity and minimize fatigue stresses.
In matting parts, the, sharper thread angles, which are used in V-shaped threads ensure higher thread engagement. The more engagement of teeth enhances the load-bearing capacity, torque transfer, and strength of the parts. The sharpness of the thread angles enhances the strength interlocking mechanism, which increases the stability and prevents any slipping, which enhances the overall durability of the machines. However, shallow threaded angles, which are used in square teeth are ideal for optimizing frictionless losses and maximizing efficiency. These teeth are not suitable for applications where threads have to bear heavy loads and high tensile forces.
If we talk about profile optimization, buttress threads, and trapezoidal threads profiles are mostly used. Buttress threads provide excellent resistance to axial loading conditions. They are ideal for screw jacks and hydraulic cylinders. Whereas, trapezoidal threads have wider flanks and larger root radii. These characteristics make them a suitable choice for power transmission applications. The manufacturing process of these profiles needs a high level of precision and accuracy.
So, CNC machines having multi-axis tooling feasibility are mostly used for milling, turning, and drilling operations. Along that rolling process is also used for mass production criteria. In the rolling process, the threads are formed by passing the workpiece, from the different dies. Rolling And CNC machining both are highly efficient for excellent surface finish and durability.
Conclusion
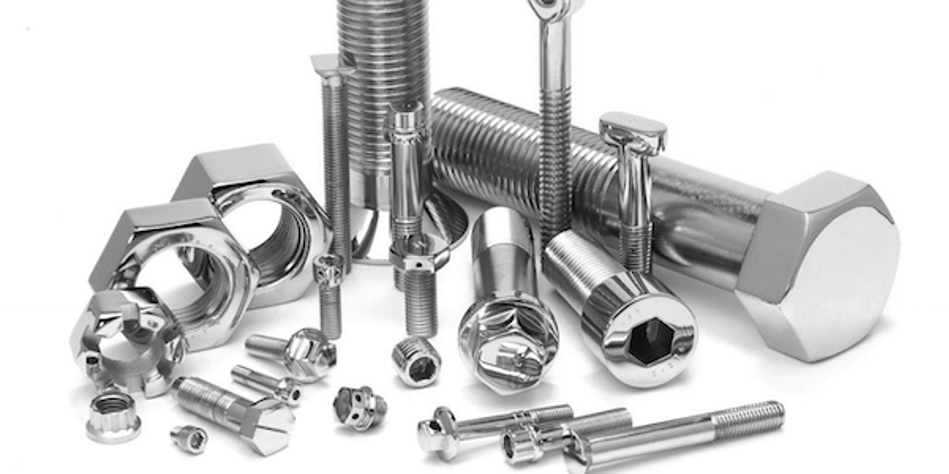
Threading precise holes needs experience and the right machining services for the strength and effectiveness of the threaded holes. So along with considerations related to materials and profile optimization, experienced engineers are a must for creating your designs. Mostly metal CNC machining services need to make threaded holes. So before choosing your machine shop for your next project, you should consult with some experts for the right decision.
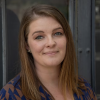
Lynn Martelli is an editor at Readability. She received her MFA in Creative Writing from Antioch University and has worked as an editor for over 10 years. Lynn has edited a wide variety of books, including fiction, non-fiction, memoirs, and more. In her free time, Lynn enjoys reading, writing, and spending time with her family and friends.