Co-extrusion is simply defined as the process of pressing two or more materials through a mold to produce a single part.
The process originated due to the need for this type of processing, particularly in the service industries. It is an advanced version of extrusion: it takes raw plastic and, after melting it, introduces it into a mold via an extruder. In this way, the plastic solidifies and becomes a continuous piece. It is useful for making products such as pipes, window frames and even fences or bridge railings.
Coextrusion takes this process a step further. Instead of melting plastic and feeding it into an extruder, two materials are used. Each goes into its own extruder and the contents melt into the mold. Through the careful placement of holes in the extruder, the manufacturer can control how the materials mix and how many layers of material are formed. It should be noted that you need a specialist to complete the coextrusion process properly. It requires a high level of technical expertise. It takes skill and experience to set the extruders correctly and ensure the two materials sit properly in the mold, allowing them to interlock before they cool and become one.
What is an extruder?
An extruder is simply a machine designed to receive material and force it through an opening. The opening is shaped to ensure the creation of a specific design, such as a piece of pipe or a window frame. It handles a material and creates a product. It is an older technology than co-extrusion, simple to use and produces a single layer of plastic.
Coextrusion, on the other hand, produces multiple layers, requires a significantly higher level of expertise and can be more expensive to create the profile. However, the parts produced are often cheaper than those made from a single raw material.
Why use coextrusion?
The coextrusion process came about as industries needed stronger and more versatile solutions.
The addition of additional layers adds strength to the final mold. More importantly, pressing the materials together allows the final piece to have specific qualities. For example, a softer plastic player can have a waterproof coating. Alternatively, it can be heat-sealed or impermeable. The properties of a co-extruded product can be vastly different to the properties of the original material.
In many cases, the co-extruded product is stronger and more durable than the original product.
Examples of coextruded products
Co-extrusion is used to make many of the products we see and use in our daily lives. These include PVC pipes, plastic bags and even plastic insulation wire. The process is also used to make shutters, decking, fence posts, water tanks and even drinking straws.
Although co-extrusion is associated with plastic products, it can be an environmentally friendly solution as the process can be used with recycled plastic, minimizing environmental impact. This approach can also help minimize the production costs of these products.
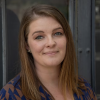
Lynn Martelli is an editor at Readability. She received her MFA in Creative Writing from Antioch University and has worked as an editor for over 10 years. Lynn has edited a wide variety of books, including fiction, non-fiction, memoirs, and more. In her free time, Lynn enjoys reading, writing, and spending time with her family and friends.