Modern industries can depend on powder metallurgy (PM) for faster product delivery without worrying about quality, supply, and cost factors. This technique is specifically relevant to the automotive sector. This sector can rely on PM more than traditional metalworking methods because it offers excellent material composition, traits, intricate shapes, and much more at an affordable price while being environmentally responsible. There are plenty of reasons why this innovative method is considered greener and cost-effective.
Powder Metallurgy: Greener and affordable manufacturing method
This specific manufacturing process helps reduce waste, repeat complex shapes, and create lightweight components, which greatly benefit automobile makers. Plus, the solutions are also offered at a reasonable cost. For an idea, you can explore BLUE powder metallurgy products. You can browse options like bushings, bearings, gears, sprockets, filters, exhaust systems, brake parts, structural components, etc. Some vendors also offer customization to meet clients’ specific requirements. Each of these products is made through sustainable efforts.
1. Waste minimization
Powder metallurgy processes can make near-net-shape or net-shape forms, reducing the need for more material inputs. Due to material efficiency, this practice becomes both environmentally friendly and cost-effective.
2. Replication of complex lightweight parts
PM manufacturing companies use tailor-made alloys obtained through powder blending. You cannot achieve this through melting, especially when different materials have varying melting points. So, the ability of PM methods to produce unique material compositions using distinctive alloys makes them outstanding. You cannot rely on traditional methods for this.
3. Manufacturing of lightweight components
Through repeatable production, components with even complex shapes can be obtained. These tend to be stronger, too. This reduces machining requirements and material waste tremendously. If you need consistent and lightweight parts for your vehicles to improve their fuel economy and emissions, you cannot overlook this aspect.
4. Affordable Solutions
No manufacturing process can receive its due credit without considering its cost-effectiveness. Less dependence on secondary processes immediately affects the production cost positively. Plus, products feature excellent dimensional control, meeting desired engineering goals. All these factors eventually culminate into a low-cost but high-quality product. Do you want to experience this? Check a sintered oil pump rotor for an idea.
How is the oil pump rotor made?
This part is used in combustion engines to improve oil circulation, enhancing the lubrication required for engine performance. These parts are produced following a thorough PM manufacturing process. It starts with selecting metal powders, a mix of steel, or some other materials. The powdered metal undergoes a compaction step to achieve the right design or geometry. After this, the rotor blanks are exposed to sintering temperatures that are less than the melting point. During this temperature treatment, the metal particles solidify and leave porosity. They get higher density, further elevating their mechanical power and structural integrity. The rotors can be given their perfect form and finish in the next stage. The surface properties of this product can be enhanced through nitriding and coating techniques. Finally, balance and quality are tested.
Most automakers leaning towards green initiatives opt for PM components. It is the easiest and most lucrative way to reduce one’s carbon footprint and be more eco-conscious. You can also embrace these products to enjoy all the benefits.
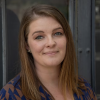
Lynn Martelli is an editor at Readability. She received her MFA in Creative Writing from Antioch University and has worked as an editor for over 10 years. Lynn has edited a wide variety of books, including fiction, non-fiction, memoirs, and more. In her free time, Lynn enjoys reading, writing, and spending time with her family and friends.