The manufacturing industry is facing a major challenge as many factories rely on outdated equipment. These older systems drive up operational costs, adding to concerns about energy waste and its effect on productivity and budgeting. To stay competitive and cut expenses, factories need to invest in energy-saving upgrades that align with modern industry standards.
Switching to energy-efficient technology brings noticeable benefits for factories moving away from outdated systems. The best approach involves exploring different solutions, from better industrial track lighting to smart monitoring systems, all aimed at cutting waste and improving efficiency. Strategic upgrades not only lower operational costs but also future-proof facilities against rising energy demands and stricter regulations.
Upgrading Industrial Track Lighting to Reduce Energy Waste
Old lighting systems in factories waste energy, leading to high utility bills. Upgrading to modern industrial track lighting solves this problem by offering better visibility while using less power. Facilities that adopt these systems benefit from lower costs and a well-lit workspace that boosts productivity. LED track lighting, for instance, can cut energy consumption by up to 60% while providing superior brightness and a longer lifespan compared to traditional fixtures.
Modular and adjustable track lighting adds flexibility, making it easy to adapt to changing production layouts without major renovations. When selecting replacements, energy ratings matter since they show how efficient the system is. A well-planned installation maximizes performance, helping factories create more adaptable and cost-effective workspaces.
Retrofitting Machinery with Variable Frequency Drives (VFDs)
Fixed-speed motors in older factories use more power than necessary, increasing operational costs. Retrofitting machines with Variable Frequency Drives allows motors to adjust speed based on real-time needs, improving efficiency and cutting energy waste. This upgrade not only lowers costs but also aligns operations with modern energy standards.
VFDs offer more than just energy savings. They reduce maintenance costs and extend equipment lifespan. A careful evaluation of existing systems and correct installation methods help factories get the most out of this upgrade, particularly when integrating VFDs with older equipment. Some factories have reported energy savings of up to 30% after implementing VFDs, making a significant impact on overall operational expenses.
Sealing Compressed Air Leaks to Stop Energy Waste
Compressed air systems in older factories often have hidden leaks that quietly waste energy. These leaks lead to higher operational costs, affecting the factory’s bottom line. Even small leaks add up over time, increasing energy losses that may go unnoticed until the bills arrive. Studies have shown that a single quarter-inch leak in a compressed air system can cost a factory thousands of dollars annually in wasted energy.
Finding and fixing leaks is key to controlling energy use. Ultrasonic leak detectors help identify problems before they get worse. Smart monitoring technology enhances this process by providing real-time data, making it easier to stay on top of maintenance. Regular inspections help maintain air pressure, extend equipment lifespan, and create a more energy-efficient work environment.
Installing Smart Power Distribution Systems for Better Load Management
Aging electrical systems in factories can lead to hidden energy waste and safety risks. Older setups often struggle to meet modern demands, driving up costs. Smart power distribution systems solve these issues by allowing factories to manage energy loads efficiently and improve overall performance.
Real-time monitoring in these systems helps identify inefficiencies and pinpoint where older machines fall short. Upgrading electrical panels and using adaptive busways creates a flexible infrastructure that adjusts to changing operational needs. Taking a step-by-step approach to these upgrades helps factories improve energy management while minimizing disruption.
Automating HVAC Systems to Cut Heating and Cooling Costs
Many older factories rely on HVAC systems that run continuously without considering actual needs, leading to high utility costs. These systems can be made more efficient through automation that integrates occupancy-based sensors. Adjusting climate control in real-time allows factories to cut down on unnecessary energy use.
Better HVAC efficiency is also achieved by adding insulation and using zoning techniques. Isolating different areas helps factories maintain the right conditions for various processes. These changes not only cut energy costs but also improve air quality. Regular HVAC checkups open the door for ongoing improvements in efficiency.
Upgrading factory equipment saves money, improves productivity, and cuts energy waste. Better track lighting improves visibility while lowering power bills. Variable Frequency Drives help machines use only the energy they need, reducing costs and wear. Fixing air leaks stops factories from throwing money away on wasted energy. Smart power systems make it easier to manage electricity use and avoid overloads. Automated HVAC systems adjust heating and cooling based on actual needs, cutting waste. Simple changes like insulation and zoning improve efficiency even more. Taking these steps helps factories run smoother, stay competitive, and keep costs under control.
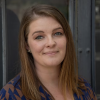
Lynn Martelli is an editor at Readability. She received her MFA in Creative Writing from Antioch University and has worked as an editor for over 10 years. Lynn has edited a wide variety of books, including fiction, non-fiction, memoirs, and more. In her free time, Lynn enjoys reading, writing, and spending time with her family and friends.