It is well known that PLC (Programmable Logic Controller) is widely used in the control of various production lines, such as in the automotive, electronics, and machinery industries.
PLC can achieve automatic control of various production processes on production lines, such as automatic assembly, processing, packaging, handling, and inspection, thereby improving production efficiency and reducing labor costs. For example, in the automotive industry, PLCs are used in body welding production lines to automatically control and adjust the welding process, improving both production efficiency and quality while reducing labor expenses.
PLC can also be applied in smart building systems for energy management, security monitoring, lighting control, and building automation, creating an energy-efficient, safe, and comfortable environment. For instance, PLCs can control building energy management systems, enabling energy consumption monitoring and environmental temperature regulation, thereby increasing energy efficiency in buildings.
In smart lighting systems, PLCs can automatically adjust lighting based on human activity, enhancing indoor lighting comfort and reducing electricity costs.
Moreover, PLCs are extensively used in building material production projects.
(1) Control of Equipment Movement:
PLCs can control various moving parts in building material production equipment, such as conveyor belts, mixers, vibrating machines, and cutting machines. Through programmed control, PLCs ensure precise movement, guaranteeing accuracy and consistency in the building material production process. For example, in concrete mixing plants, PLCs are used to control and monitor the entire production process, automating tasks like material feeding, mixing time, and speed control, as well as discharge, to ensure the quality and consistency of concrete.
(2) Temperature and Humidity Control:
In processes such as concrete pouring and brick baking, temperature and humidity are critical parameters. For instance, rebar processing equipment, used for bending, cutting, and shaping steel bars for construction, relies on PLCs to control operation, angle, and size adjustments to ensure precision and consistency in rebar processing, thus improving production efficiency. PLCs can connect to temperature and humidity sensors and automatically adjust heating, cooling, and humidity control equipment based on preset control logic to ensure the quality and stability of building materials.
(3) Liquid Level and Flow Control:
In the production of liquid building materials, such as paints, glues, and adhesives, controlling liquid levels and flow is vital. PLCs can monitor and control data from level and flow sensors and regulate liquid dispensing and mixing ratios with precision based on preset logic.
(4) Data Collection and Monitoring:
PLCs can collect and process data related to the building material production process, such as temperature, humidity, liquid levels, flow, and equipment status. Through communication with other devices or upper-level systems, PLCs transmit data to operators or management systems, enabling real-time monitoring, production reporting, and quality analysis.
(5) Fault Detection and Alarm Systems:
PLCs monitor the working status and faults of building material production equipment. When abnormalities or malfunctions are detected, the PLC can issue alarms and take corrective measures, such as stopping the equipment, adjusting parameters, or switching to backup equipment, to prevent further damage or production disruptions.
(6) Automation and Efficiency:
PLCs enable automation in building material production equipment, reducing manual intervention and increasing production efficiency. Through programming and logic control, PLCs can perform various automated tasks, such as automatic feeding, mixing, and cutting. For example, stone cutting machines, often used for cutting marble, granite, and quartz slabs, rely on PLCs to control feed rates, tool positioning, and pressure for precise cutting operations. Programmed control improves both production efficiency and product quality, ultimately reducing labor costs, enhancing efficiency, and ensuring product consistency.
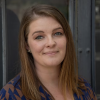
Lynn Martelli is an editor at Readability. She received her MFA in Creative Writing from Antioch University and has worked as an editor for over 10 years. Lynn has edited a wide variety of books, including fiction, non-fiction, memoirs, and more. In her free time, Lynn enjoys reading, writing, and spending time with her family and friends.